In the dynamic landscape of commercial real estate, HVAC systems play a pivotal role in maintaining a comfortable and healthy environment. The changing climate patterns have only intensified the need for efficient and reliable HVAC systems. Regular maintenance of these systems is crucial for several reasons: it leads to significant energy savings, prolongs equipment life, and ensures better air quality. The U.S. Department of Energy estimates that effective operations and maintenance of commercial HVAC systems can save organizations 5-20% annually on energy bills.
Quick access:
Understanding commercial HVAC systems
Types of commercial HVAC systems and their maintenance
The importance of commercial HVAC maintenance
Data-driven strategy for HVAC maintenace
Common HVAC maintenance mistakes
Calibration and optimization of HVAC systems
Sustainability practices in HVAC maintenance
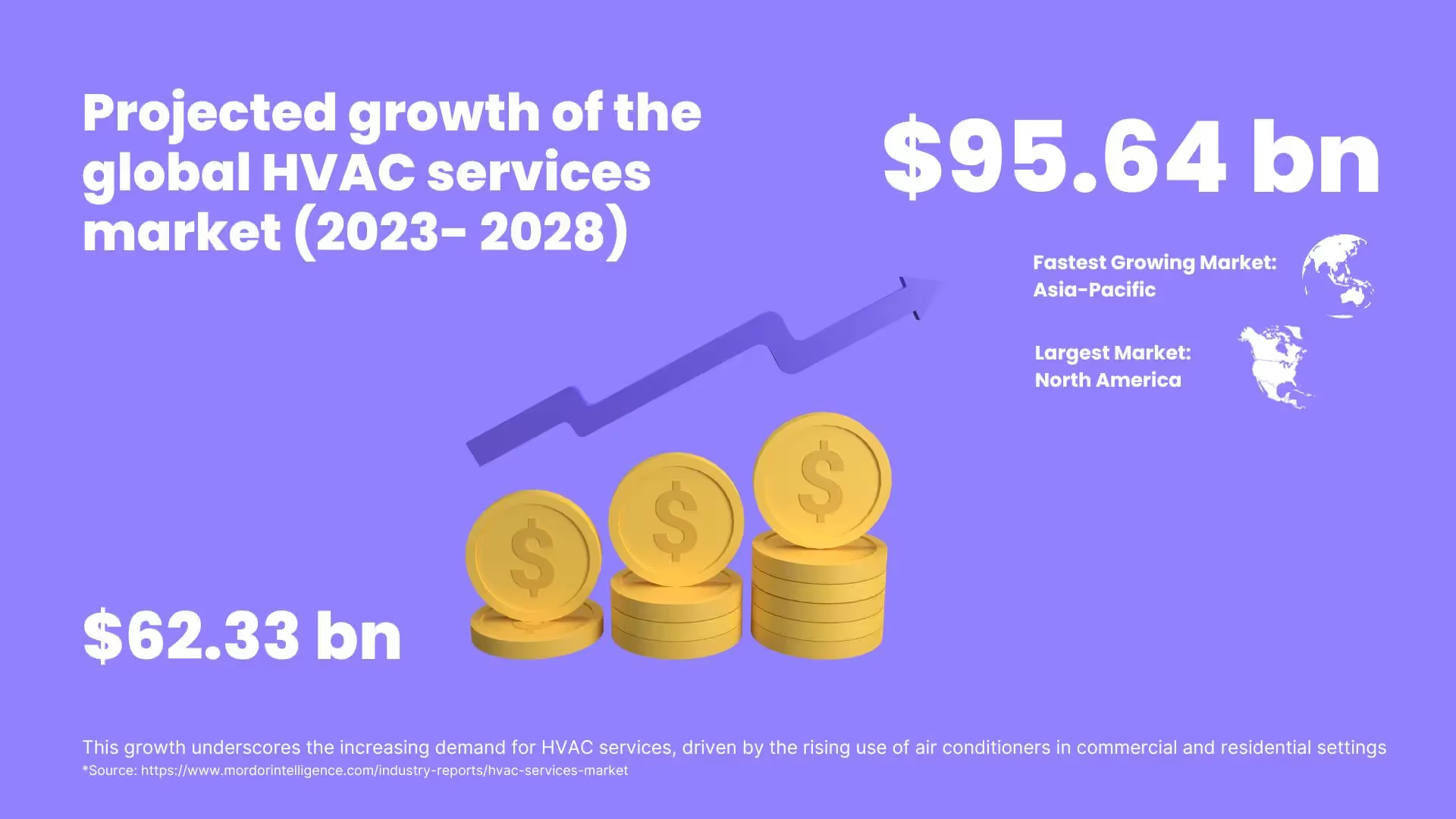
Understanding commercial HVAC systems
HVAC systems in commercial buildings are more than just temperature control units; they are integral to maintaining a healthy, comfortable, and productive environment. The systems are designed to manage the internal climate and air quality of large spaces efficiently and are essential for both day-to-day comfort and long-term property management.
Core components of commercial HVAC Systems
Here are the primary components of a commercial HVAC system, including chillers:
1. Chillers: Chillers are the backbone of any large commercial HVAC system, producing cold water distributed to air cooling coils via a pipe network. There are two types of chillers:
- Air-cooled chillers, which are typically located outside and release heat absorbed from the chilled water to the outside air.
- Water-cooled chillers, which are usually situated inside a building and release heat absorbed from the chilled water to a secondary water loop that dissipates the heat through a cooling tower.
2. Boilers: Boilers are the heating component, generating hot water or steam that is sent through pipes to radiators or convectors, which distribute the heat in the desired spaces.
3. Air Handling Units (AHUs): These units are large boxes containing a fan, filters, and heating/cooling elements. AHUs circulate air throughout the building, and their size and complexity can vary greatly based on the building's requirements.
4. Ductwork: Ducts are conduits responsible for the distribution of air throughout the building. They are designed to deliver and remove air efficiently and quietly, ensuring a uniform temperature across different areas.
5. Vents: Air vents allow conditioned air to enter a room and can be adjusted to control the flow of air. Return vents draw air out of the space to be reconditioned in the AHU.
6. Thermostats: These are the control systems that allow users to set the desired temperature. In commercial buildings, they're often part of a larger Building Automation System (BAS) for centralized control.
7. Filters: Filters clean the air that circulates through the HVAC system, removing dust, pollen, and other particulates. They are critical for maintaining indoor air quality and preventing the buildup of debris in the system.
8. Refrigerant lines: These lines carry the refrigerant substance to the air conditioning system, which absorbs heat from the indoor air and transfers it outdoors.
9. Compressors: A compressor is part of the air conditioning system that raises the temperature and pressure of the vapor refrigerant that leaves the evaporator coil.
10. Condensers: This component releases the heat from the refrigerant into the outside air for an air-cooled system, or to the water for a water-cooled system.
11. Expansion valves: These valves regulate the amount of refrigerant flowing into the evaporator, which helps in controlling the cooling process.
12. Cooling towers: Mostly used in conjunction with water-cooled chillers, cooling towers extract waste heat to the atmosphere through the cooling of water to a lower temperature.
Each of these components plays a vital role in the functionality and efficiency of a commercial HVAC system. Regular maintenance of these components is necessary to prevent system failure, ensure efficiency, and maintain a comfortable and safe indoor environment for building occupants.
Types of commercial HVAC systems and their maintenance needs
With a clear understanding of the components that make up commercial HVAC systems, we can transition to examining the various types of systems in use today and their unique maintenance requirements. Each type of system, from single-split to VRF/VRV, serves different building needs and consequently demands a tailored approach to upkeep.
- Single-Split Systems: These are the simplest type, where each indoor unit is connected to an outdoor unit. They are cost-effective for smaller spaces such as individual rooms or small offices.
Maintenance for single-split systems involves regular cleaning of filters, checking refrigerant levels, ensuring the outdoor units are clear of debris, and inspecting the electrical components for signs of wear.
- Multi-Split Systems: In multi-split systems, multiple indoor units are connected to a single outdoor unit. This allows for individual temperature control in different rooms while being more space-efficient.
Maintenance for multi-split systems requires all of the same care as single-split systems, but with added attention to the complex pipework and electrical connections. Technicians must also ensure that the failure of one component does not affect the entire system.
- Variable Refrigerant Flow (VRF) or Variable Refrigerant Volume (VRV) Systems: These are sophisticated systems designed for larger spaces such as hotels, office buildings, or shopping centers. They offer precise temperature control and high energy efficiency.
Maintenance for VRF/VRV systems is more complex due to their advanced technology. It includes checking the integrity of electronic control systems, ensuring the correct operation of inverters and variable speed drives, and routine inspections of the refrigerant circuit to prevent leaks.
The Importance of commercial HVAC maintenance
The backbone of a commercial HVAC system's longevity is routine maintenance. Regular upkeep is vital for ensuring system efficiency and reliability, which in turn, leads to reduced operational costs, minimized downtime, and a comfortable environment for occupants. Not only does it maintain the health of the system, but it also plays a crucial role in energy conservation, with proactive maintenance being one of the most cost-effective methods to decrease energy consumption and increase the lifespan of the system.
Main maintenance strategies for commercial HVAC
There are four cornerstone strategies for commercial HVAC maintenance:
- Planned Maintenance: This involves scheduled checks and services based on a predetermined timeline. It includes routine inspections and servicing tasks, typically following the manufacturer's guidelines.
- Preventive Maintenance: More comprehensive than planned maintenance, this approach includes regular and systematic checks. Key activities involve cleaning components, replacing filters, and checking refrigerant levels. Its primary goal is to maintain system health and prevent failures.
- Predictive Maintenance: Utilizing the actual condition of the equipment, this strategy forecasts when maintenance should be carried out. It relies on continuous monitoring and physical inspections to predict potential system failures.
- Data-Driven Maintenance: As the most advanced strategy, data-driven maintenance uses real-time data, analytics, and automation to predict and preempt equipment failures. This proactive approach leverages historical data trends and predictive algorithms to optimize maintenance actions, making it an increasingly preferred method in modern facilities management.
Data-driven maintenance: The key to commercial HVAC equipment longevity
Data-driven HVAC maintenance represents a paradigm shift in how we approach the upkeep of commercial HVAC systems. This method employs advanced analytics, IoT technology, and real-time data to monitor the health and performance of HVAC units proactively. By analyzing patterns and trends, it enables predictive maintenance, where issues can be identified and addressed before they escalate into major problems.
The core of data-driven maintenance lies in its ability to utilize large amounts of data from various sources – including sensors, system logs, and user inputs – to gain a comprehensive understanding of the system's health. This approach helps in:
- Predicting Failures: By monitoring system performance and identifying anomalies, it can predict potential breakdowns before they occur.
- Optimizing Operations: It enables fine-tuning of the system for optimal performance, ensuring that the HVAC operates efficiently and conserves energy.
- Extending Equipment Life: Proactive maintenance can significantly extend the lifespan of HVAC components by preventing excessive wear and tear.
One of the leading solutions in this field is CIM’s PEAK platform. PEAK offers a robust framework for implementing a data-driven maintenance strategy. It integrates seamlessly with existing HVAC systems to provide real-time insights and analytics, empowering facilities managers to make informed decisions about maintenance and operations.
For those interested in delving deeper into the nuances of this approach, CIM offers a comprehensive "Guide to Data-driven Maintenance." This guide provides valuable insights and best practices, helping users understand how to leverage data-driven strategies effectively for their HVAC systems.
.jpg)
Data-driven maintenance is not just about preventing breakdowns; it’s about redefining the approach to HVAC system care. By transitioning to this advanced method, commercial buildings can ensure their HVAC systems are not only more reliable and efficient but also more aligned with modern operational demands.
Common HVAC maintenance mistakes
Avoiding common HVAC maintenance mistakes can save commercial facilities from incurring unnecessary costs and downtime. Some of the prevalent mistakes include:
- Neglecting Regular Maintenance: Skipping routine check-ups can lead to a buildup of problems that could have been easily avoided with regular maintenance.
- Ignoring Early Warning Signs: Small irregularities, like unusual noises or slight performance drops, can signal bigger issues. It's essential to investigate these signs promptly.
- Improper Calibration: Failing to correctly calibrate thermostats and sensors can lead to systems running more often than needed, increasing wear and raising energy costs.
- Forgetting to Replace Filters: Dirty or clogged filters strain HVAC systems, reduce air quality, and decrease efficiency. Regular replacement is a simple yet often overlooked task.
- DIY Repairs Without Expertise: While some maintenance tasks can be handled in-house, more complex repairs should be left to professionals to avoid further damage.
- Overlooking Duct Maintenance: Leaks or blockages in ductwork can severely impact system efficiency. Regular inspections are necessary to ensure ducts are in good condition.
By understanding and circumventing these common errors, building owners and facilities managers can ensure their HVAC systems are not just operational but optimized for peak performance. It's a proactive approach that aligns perfectly with the principles of data-driven maintenance—anticipating needs and addressing them before they escalate into significant issues.
Calibration and optimization of HVAC systems
Integrating the importance of calibration and optimization into the broader discussion of commercial HVAC maintenance, we find that these processes are fundamental to achieving and maintaining the efficiency of HVAC systems. In fact, the Alliance to Save Energy highlights that heating and cooling efficiency is among the most effective ways to decrease overall energy consumption in commercial buildings, with the U.S. Small Business Administration noting that HVAC equipment accounts for about 40 percent of energy usage in such buildings. This underscores the importance of calibration, which ensures that HVAC systems operate within their optimal parameters, adapting to the needs of the space and the preferences of the occupants.
Calibration is the process of fine-tuning HVAC systems to ensure they operate according to the designed parameters and respond accurately to the building's temperature and humidity requirements. This precise adjustment is crucial for performance because it affects how well the system can maintain the desired indoor environment, directly impacting energy efficiency and occupant comfort.
A well-calibrated system will keep the building at the set temperatures, avoiding unnecessary energy consumption. For example, a miscalibrated thermostat could cause the system to run longer than necessary or not engage when needed, resulting in higher energy bills, lower sustainability score and wear on the system.
The best practice for recalibrating HVAC systems is to align it with the changes of the seasons. At a minimum, recalibration should occur biannually, ahead of the heating and cooling seasons. However, in regions with significant temperature fluctuations, more frequent checks may be warranted. For instance, during a heatwave or an unexpected cold snap, systems may need additional adjustments to handle the extreme conditions effectively.
Understanding the significant impact of HVAC systems on a building's energy profile, it becomes evident that calibration and optimization are not just about maintaining operational efficiency; they are also about embracing sustainability. As we pivot from the technical aspects of HVAC management to its environmental implications, the focus on sustainability becomes paramount.
Sustainability practices in commercial HVAC Maintenance
The meticulous maintenance of HVAC systems plays a pivotal role in the sustainability practices of commercial buildings. It is through diligent care—including calibration, optimization, and regular upkeep—that these systems can operate at peak efficiency, conserving energy and reducing the building's carbon footprint.
The integration of HVAC maintenance with sustainability initiatives is particularly evident when considering the prerequisites for green building certifications like LEED or NABERS. These certifications evaluate a building's environmental impact, and a well-maintained HVAC system is often a critical component in meeting their standards.
For example, HVAC systems influence two scoring categories that together comprise 40 percent of the total LEED points: Energy and Atmosphere (EA), which can contribute up to 38 points, and Indoor Environmental Quality (IEQ), worth up to 21 points.
Effective HVAC maintenance can directly lead to improved energy performance, which is a key metric in these certifications.
By aligning HVAC maintenance with sustainability goals, commercial buildings not only enhance their operational efficiency but also contribute to a larger movement towards environmental responsibility and stewardship. This commitment to sustainability through conscientious HVAC maintenance is becoming an industry standard, reflecting the evolving expectations of occupants, businesses, and society at large.
Navigating legal and compliance aspects of commercial HVAC maintenance
Understanding and adhering to the legal and regulatory requirements of commercial HVAC maintenance is essential for facility managers and business owners. This ensures not only the legal operation of their properties but also guarantees the safety and well-being of occupants. Adherence to these requirements, which range from local and federal laws to international standards, addresses crucial issues such as safety protocols, energy efficiency measures, and environmental protection.
Key legal and compliance aspects in HVAC maintenance:
- Building Codes: These vary by location and mandate standards for the safe operation and maintenance of HVAC systems. They include specifications for system capacity, ductwork, ventilation, and more, often based on guidelines from the American Society of Heating, Refrigerating, and Air-Conditioning Engineers (ASHRAE).
- Energy Efficiency: Regulations often stipulate minimum energy efficiency levels for commercial HVAC systems. These can include the use of high-efficiency equipment, controls for managing energy usage, and regular maintenance to maintain system efficiency.
- Environmental Regulations: The Environmental Protection Agency (EPA) regulates the use and management of refrigerants due to their impact on the ozone layer and climate change. This includes proper refrigerant handling and disposal procedures.
- Fire Safety: Fire codes regulate the placement of HVAC units, the installation of fire dampers in ductwork, and the maintenance of ventilation systems to prevent the spread of fire.
- Triple-Net Lease Agreements: Especially relevant in the retail and industrial sectors, these agreements often establish HVAC maintenance guidelines for commercial real estate (CRE) properties. Compliance with these terms is essential to avoid noncompliance issues.
- Vendor Service Tickets: Ensuring compliance through vendor service tickets is crucial. Property managers should not mistake vendor contracts as proof of compliance, as the actual maintenance can only be proven through a vendor service ticket.
- Equipment Inventory: Effective management of an HVAC unit requires a comprehensive understanding of its components, including make, model, expected lifespan, and maintenance history.
- Automated Tracking Systems: Automating maintenance requests can streamline compliance tracking. This allows property teams to send maintenance report requests on a regular schedule and ensures proper upkeep.
- Vendor Management: Property managers should provide a list of vetted vendors for tenants. This helps in managing and evaluating suitable vendors for HVAC maintenance, ensuring that maintenance standards are met.
- Data Visualization Tools: Utilizing HVAC management software with data visualization tools aids in tracking tenant compliance and identifying areas of noncompliance efficiently.
For more detailed information on HVAC standards and guidelines, including Standard 180 which establishes minimum HVAC inspection and maintenance requirements, you can refer to ASHRAE's resources at ASHRAE Standards and Guidelines.
These legal and compliance aspects are essential for the effective operation of HVAC systems in commercial buildings, ensuring not only the comfort and safety of occupants but also the legal and operational integrity of the business.
Conclusion: Navigating the future of commercial HVAC maintenance
In summary, the role of HVAC systems in commercial real estate has never been more critical. From ensuring energy efficiency and prolonging equipment life to maintaining high indoor air quality, the benefits of regular HVAC maintenance are manifold. By understanding the different types of systems and their unique maintenance needs, and adopting strategies like planned, preventive, predictive, and data-driven maintenance, facilities can significantly enhance their operations.
Data-driven maintenance, particularly through platforms like CIM’s PEAK, stands out as a forward-thinking solution. It empowers facilities managers with real-time insights and analytics, enabling proactive maintenance and operational decisions.
We encourage you to embrace the future of HVAC maintenance by implementing data-driven strategies and considering the adoption of CIM’s PEAK platform for your buildings.