A commitment to occupant comfort, workflow management and sustainable processes underpinned the deployment of CIM’s PEAK Platform at a multi-tenant building in Dublin Landings - a 10-story, 13,000 sqm office building located in Dublin city centre.
Since deploying CIM’s PEAK Platform, Burlington has increased employee and visitor comfort levels, improved equipment performance, and streamlined Contractor maintenance and repair workflows. All this was achieved while driving sustainability goals, lowering energy usage and reducing CO2 output.
Key Partnership Wins
- €62K realised energy savings in 2022
- 13K square metres of office space optimized
- 128 workflow actions identified at a closure rate of 68%
- 558 pieces of equipment monitored
- 1,017 FDD rules deployed
- 97% thermal comfort score
About Burlington
With over 40 years’ of experience, Burlington are leaders in mechanical, electrical and HVAC control systems. Their clients include Oracle, government bodies and CBRE. Burlington are committed to sustainability and environmental management. They work with clients to achieve both Leadership in Energy and Environmental Design (LEED), WELL Building Standard and ISO 50001 accreditation projects.
Burlington has embraced digital transformation, placing building analytics at the forefront of all building operations to help their clients operate at peak operational efficiency. Through data-driven decisions, their service prioritises the health, wellbeing and comfort of the employees in, and visitors to, the buildings in their care.
"Burlington prides itself on being one of the highest quality building services engineering providers. The financial performance, operational efficiency and drive towards a more sustainable future are key priorities for our team.
CIM’s PEAK Platform is a key enabler when it comes to delivering this for our clients. By deploying the latest technology on our client sites, they are guaranteed a service at the cutting edge of digital innovation.”
Stuart Gaffney
Corporate Account Mgr and Associate Director, Burlington
Partnering for Success
CIM partnered with Burlington in July, 2021 when the PEAK platform was deployed on a 10-story, 13,000 sqm office building close to Dublin docks, also referred to as Silicon Docks due to the high concentration of tech companies.
Since the initial deployment of the PEAK Platform, the partnership between CIM and Burlington has only grown stronger. Given the improved occupant comfort, better team collaboration and increased operational efficiency at the multi-tenant building in Dublin Landings, Burlington is now looking to roll out PEAK across other high profile client sites.
Occupant Comfort
The thermal comfort of both occupants and visitors are extremely important to Burlington. Since deploying PEAK on the building, the occupant comfort level increased from an already impressive 91% to an almost perfect score of 97%. The metric itself is calculated by measuring how often the indoor temperature stays at the median value of a set range.
238 sensors feed information from the building management system (BMS) through to PEAK for constant monitoring. Facility Managers and Contractors can quickly see the current status of the building’s thermal comfort rating by accessing the “Indoor Environment” tab in PEAK on any device.
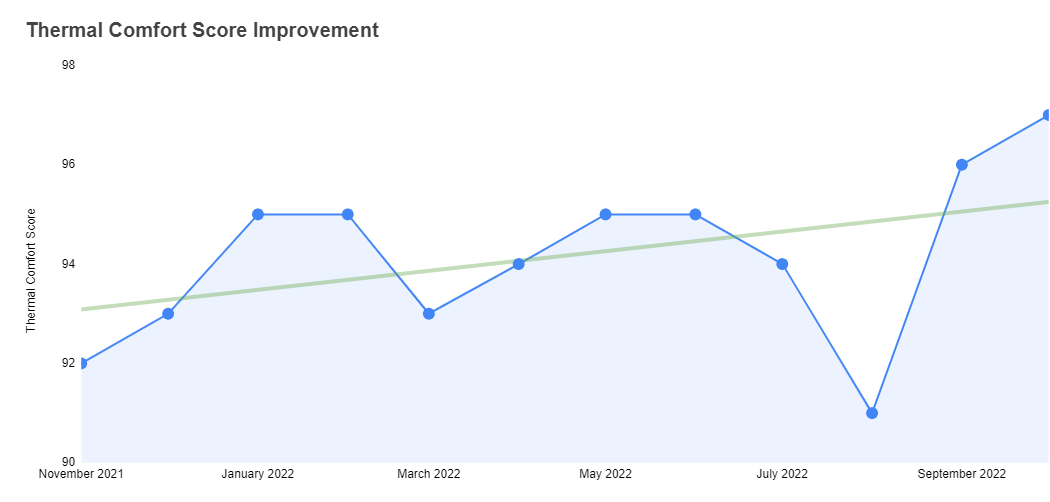
“Many factors determine the ideal temperature for a commercial building. Poor thermal comfort caused by faulty equipment can be a major source of inefficiency. The PEAK Platform empowers our team to monitor zones and quickly resolve any issues that may arise. When building occupants are comfortable and satisfied, they are more productive, happier and healthier. This is the best possible outcome and a key focus for our team.”
Seamus Carr
Director of Projects, Burlington.
Team Collaboration
Six Facilities Managers and Contractors use the PEAK Platform to ensure issues are identified and resolved quickly at the multi-tenant building in Dublin Landings. The team use the platform to assign “Alerts” to the appropriate person. This ensures all team members can seamlessly collaborate in real-time to rectify any problems that may arise.
The Challenge
Issues on-site often require the input of multiple trades before they can be resolved. The traditional back-and-forth communication through emails, texts and calls could regularly slow progress. With everything captured in PEAK, the whole team has full visibility over progress related to each task and who is currently doing the work.
Previous to the implementation of PEAK, a Contractor would sometimes spend their limited time finding issues before resolving them. Now, the platform removes any guesswork and saves time by identifying the root cause and also recommends a solution. This means Contractors can use their time on site investigating the most important issues first.
How PEAK Helped
From the time PEAK was first implemented, 128 actions have been identified with a closure rate of 68%. 558 pieces of equipment are currently monitored with 1,017 rules deployed to ensure any faults are quickly brought to the attention of the appropriate person. Given the cloud-based nature of the platform, both Facilities Managers and Contractors can access this data at any time, whether on-site, working from home or on the road.
The PEAK platform has simplified the process for identifying and resolving issues at Dublin Landings. PEAK does the hard work for Contractors through automated fault detection and diagnostics (FDD). This reduces time inspecting equipment and finding faults, and results in more time spent resolving the issues identified and prioritised by PEAK.
Closing Out Actions as a Team
The graph on the next page shows the total number of actions closed out each quarter. Since PEAK was first deployed, the number of actions closed grew steadily each quarter.
Teams can effortlessly assign Alerts to the correct team member with a single tap using PEAK's Actions Manager. Once assigned, all team members can collaborate in real-time to quickly and efficiently resolve issues.
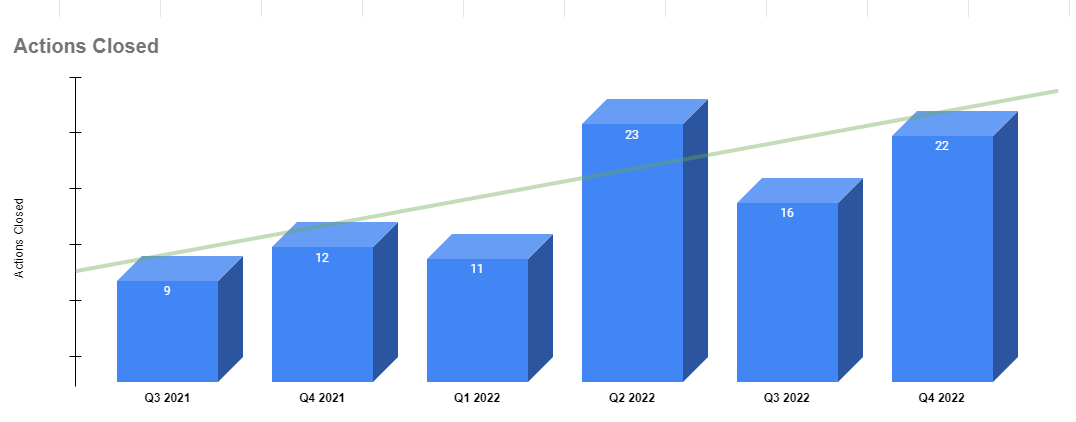
Operational Efficiency
Operational efficiency has never been more critical for Burlington, especially given their commitment to sustainable processes, stellar environmental management and the drive to net zero. On top of this, operational efficiency has a significant impact on the financial performance of any building, especially given the pressures caused by energy costs.
When Burlington first implemented PEAK at Dublin Landings, a key priority was to quickly identify and address small issues throughout the building to achieve energy savings and improved thermal comfort. 93 fan coil unit (FCU) actions have been closed out to date, each with their own inefficiencies either mechanically, electrically or issues related to control narratives. Actions closed are outlined in the graph above.
PEAK in Action
PEAK detected a piece of plant operating out of hours and automatically communicated the issue to relevant team members through the “Alerts” section in the PEAK dashboard. The piece of plant in question was a supply fan for the boiler house. This fan only activates when the boiler or combined heat and power (CHP) is enabled.
The Facility Manager on site carried out an inspection of the plant and found everything to be in order. He then reviewed the data on PEAK to verify what had enabled the boilers/CHP. This was done by charting the enable signals on all on-site equipment in the Charts section of the PEAK dashboard.
Through PEAK Charts, the Facility Manager could quickly see that the boilers were activated by the Domestic Hot Water (DWS) system being enabled. He found the time zone that enables the DHW had been set to 24/7 operation. He corrected this timezone to operate for 8 hours a day, reducing the demand by 66% overall. This had a significant impact on energy usage as the Boilers, CHP & Supply Fan along with associated pumps sets were now all disabled out of hours.
Looking to the Future
Optimisation and efficiency never ends, there is always more to be done. The Dublin Landings building was already operating at high performance. While Burlington’s implementation of PEAK has improved on this even further, their sights are firmly fixed on the next stage of optimisation. This includes rewriting control strategies, assimilating all Co2 sensors and pulling all energy meter data into PEAK across all buildings to further improve efficiency and reduce energy spend.
Outside Dublin Landings, Burlington is now looking to roll out the PEAK platform on other client sites. The intention is to get additional client sites commissioned and benefiting from the efficiencies currently seen at Dublin Landings.
CIM is dedicated to developing and building on our current partnership with Burlington in accordance with their long-term strategic digital transformation goals. The main indicator of our own success is ultimately the continued success of our clients. We are grateful and humbled to work with Burlington across their portfolio of properties, and we look forward to working together to achieve even more success in the future.
“CIM's PEAK Platform has delivered a number of wins at Dublin Landings. Energy reduction, improved occupant comfort and greater transparency of workflows and tasks to name just a few.
Our team also ironed out a number of small issues with fan coil units that resulted in a bigger overall win of improved operational efficiency.”
Stuart Gaffney
Corporate Account Mgr and Associate Director, Burlington