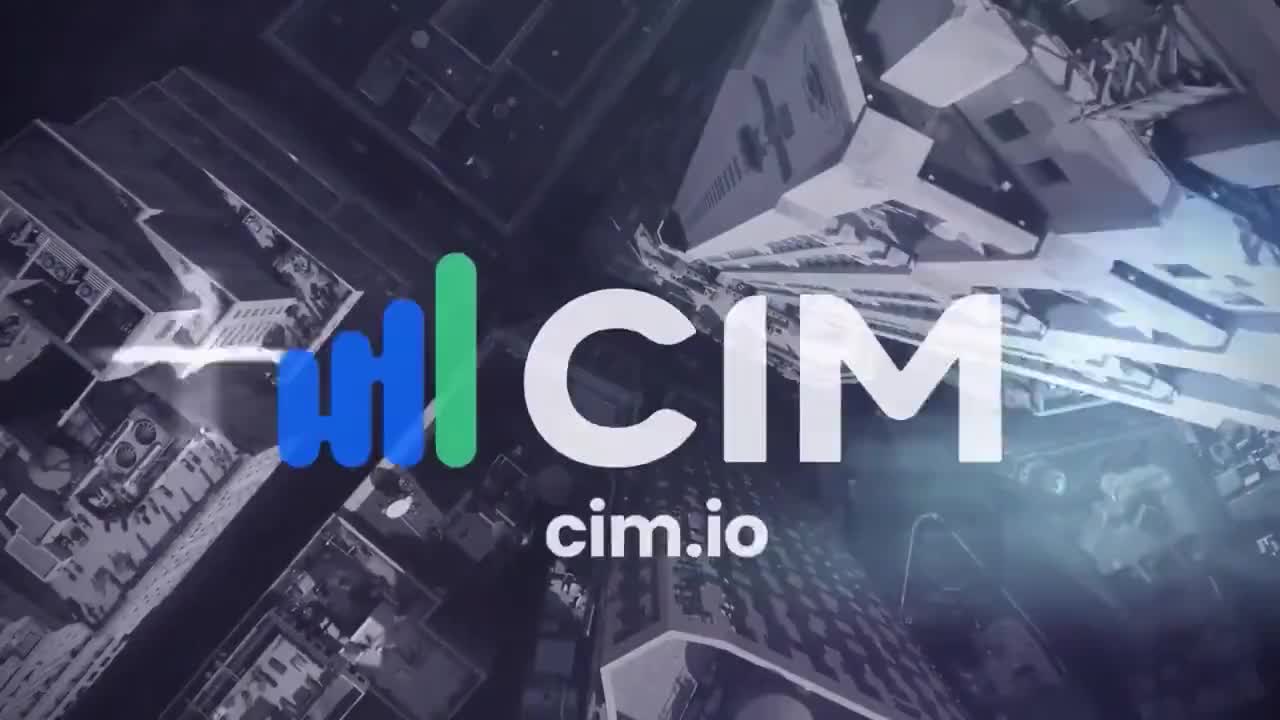
Video Transcription
Hello. My name is Paul Walsh. I work as the general manager for CIM and CIM has developed innovative software that helps people operate large, complex assets at their PEAK performance. And my objective in this case study demo is to give you an overview of how a good data analytics solution can complement or enhance or augment any companies that want to start their ISO 50001 journey.
So the agenda today is just to talk about ISO 50001, touch on some of the high points and outline what you need to start on that journey. Then touch a bit on what the implementation involves. And then maybe give you an overview of CIM and how we help clients get going on that journey, and then talk about a case study to show you some dashboards of anonymised sites that we have helped in Irish manufacturing to improve their ISO 50001 program or to get started on a brand-new certification.
So ISO 50001, it is the international standard for energy management. It does align best practices right across the globe and tries to work year-on-year on incrementally improving those in any of the sites that get certified, and it is applicable for any size organization or any type of organization.
And what you need to do, firstly, you definitely need to have an energy policy which can be quite easily drafted up. You need to establish a baseline energy targets and the objectives of the plan you want to include. Then you need to really use the data and a lot of the auditors want to see how the data is collected and how you're using that data to identify opportunities for improvement. You really need to show to them that you have a monitoring verification, so you're looking at before versus after and ensuring that the savings don't degrade over time.
And how data analytics dovetails with 50001 in our opinion is that any data analytics platform, by virtue of the fact that it needs quality data, a part of what data an analytics solution provider like CIM would do is we would collate and cleanse the data and ensure that it's being logged in 15 minute intervals, we would do some metering gap analysis for clients and once the data hygiene has been sorted, we ingest that data into a platform, and then we run fault detection diagnostics on that dataset.
A huge body of work in preparing the data is getting it in a central repository, and that is a typically a big body of work for anyone who's starting on the ISO 50001 journey. So, what we have found is the fact that we have got data out of the individual silos that resides in the building and brought it to one central place is a huge value-add to anyone starting the 50001 journey. So that's where data analytics and 50001 certainly complement each other at the very start.
We then use the data to help identify opportunities for improvement. So this is part of the fault detection diagnostics. It detects where plant and equipment is not running efficiently. So, often the low cost and the no cost opportunities fall out of the data, and they can be implemented quite effectively and quickly. You get an element of the operational control because you can put in upper and lower control limits on the data set. So when equipment begins to deviate, you can immediately act. Then it builds that M and V or the monitoring and verification, which is critically important to ensure your savings don't degrade over time.
And how the 50001 process works - it typically works on this Deming cycle where you have this plan, do, check, act philosophy, and big part of what data analytics does is around this planning bit. So, in order for companies to understand what they need to do, or where they need to deploy resources, whether it's people or money, they really need to understand where the biggest bang for the buck is. And data analytics will do that.
Typically, sites can depend on vendors or equipment manufacturers to say, "listen, the chiller is X number of years old, it needs to be replaced". Data analytics can often contradict that, and it will say "listen, that piece of equipment is running fine. If you do want to upgrade, here's a better opportunity from an energy reduction perspective and from a return on investment perspective".
The planning part of the ISO 50001 process is very much where data analytics overlays with it and enables the site to execute the biggest value projects. And again, from the auditor's perspective, they love seeing how data is informing the decisions that are being made and continuously doing so.
On the performance side, the energy performance indicators, they are called ENPI's, once the data is ingested and normalized we can put ENPIs in place that will track equipment performance and that typically blends data from multiple sources. So from your building management system and from your energy management system to get ENPIs like co-efficiency performance on a chiller. This is because you typically need flow meter data from your BMS, you might need energy meter data from your energy management system if you have that on site. Again, the monitoring refers to how the savings are maintained over time. And then improvement is that year-on-year performance improvement where you say, "okay, we've done this amount of opportunities for improvement that the data recommended, here's the additional body of work that we want to do". And then you tighten your ENPIs to make sure that doesn't deviate over time.
Some of the outcomes that clients get from our PEAK platform - you can see on the left-hand side of this slide here is the ISO 50001 type which is energy and OPEX reductions. The better environmental ratings refer to buildings that have certifications such as LEED, GRESB, WELL and that type of building energy ratings standards. We moved to data driven maintenance, so we move away from the scheduled maintenance programs to condition based maintenance. And then the site gets carbon reductions.
A lot of the large corporate clients we work with have CO2 reduction targets, and they want to achieve them. By virtue of the fact that they have been implementing ISO 50001 gives them almost an immediate demand side reduction, and you get an associated CO2 reduction as well.
On the ancillary benefits to the site, you get an element of technical engineering support, like a virtual engineering team that you didn't have in place before. You also get improved comfort or thermal conditions for your employees. For anyone who has validated spaces, you're ensuring that it's not too hot or too cold in there for them or in an office environment. You also get increased equipment lifespan because equipment is not running outside of its design parameters anymore. The data is driving those types of decisions not to stop that type of conditions occurring. And then you obviously get increased uptime because it plant and equipment is not not failing as frequently because the data is driving the predictive maintenance on it.
So what I will do now is I will pause and I will show you what the software looks like. This is CIM's PEAK Platform and our landing page shows the energy consumption and baseline consumption, which is extremely important from an ISO 50001 perspective. It shows before which are the grey columns and after which are the blue columns. Here you can see a year-on-year reduction.
For ISO 50001 certification, we need to get the energy data and break it into what's called significant energy users and visualise those in doughnut charts or in cumulative stacked column charts and track the performance of chillers and other significant compressors, significant energy users on site and report out when the consumption has gone above or below certain thresholds.
Other dashboards that we've built from an energy visualisation perspective is around energy awareness, transforming the energy from a kilowatt-hour or a gigawatt hour value into values that people might readily understand. So the number of smartphones charged or the number of trees planted or the number of barrels of oil equivalent. It just allows people on site to get their head around the energy reduction and also improves the energy literacy on site.
The other aspect of this dashboard, from an ISO 50001 perspective, is that it looks at the equipment run-hours. It shows the difference in the last weeks and average run-hours compared to the three months before that. You can see examples of when plant and equipment has changed and that anomaly is then flagged with the CIM engineering team, and we work collaboratively with the site to resolve those issues.
So this element of control, monitoring and verification of savings is a key part of the ISO 50001 standard, and it's baked into part of what the PEAK platform gives our clients. The resolution of these tickets is a close out, so from an auditing perspective there's a full circle of closures of the actions.
Thank you for your time today. I promised to keep it short and sweet, so hopefully I've lived up to that. If you have any questions, please reach out to me directly at paul.walsh@cim.io. Or we can continue the conversation by visiting CIM.io to find out more about our building analytics platform does and how we've helped some Tier 1 clients.